MATERIALS
Jacket Materials:
Ultra Seal offers a wide choice of seal jacket materials, mainly based on PTFE resins.
PTFE is resistant to most chemicals except chlorine trifluoride/fluorine gas at high temperatures and molten alkali metals. However, as many sealing applications use filled PTFE resins to improve performance, care should be taken that the filler will not be attacked by the sealed medium.
Stainless Steel and NACE approved springs are available as is a range of elastomeric energizers.
When using elastomers, consideration of temperature/chemical compatibility and life should be accounted for.
At temperatures below -40. C. PTFE and many other jacket materials will harden and shrink. This feature imposes higher loads on the energizer and may compromise sealing efficiency. Face seals (Axial Seals) are less affected than Radial Seals but we recommend our technical department be consulted for seal designs working at -40 deg. C and below.
CODE NO |
DESCRIPTION |
COL |
APPLICATION |
TEMP
(C) |
COEFF.
FRICTION |
WEAR
FACTOR |
01 |
Virgin PTFE
|
White |
Excellent for light dynamic and static service. Low gas permeability. Good cryogenic properties. FDA Approved
|
-260
+200 |
0.09
|
10000
High |
02 |
Premium PTFE
|
Blue |
Similar properties to code 01 but with improved wear resistance. |
-260
+200 |
0.09
|
150 |
03 |
PTFE/Carbon/
Graphite |
Black |
Excellent material for heat and wear resistance. Recommended for dry and poorly lubricated applications, suitable in water and stream service. |
-260
+300 |
0.09
|
10 |
04 |
PTFE/Glass/
MOS2 |
Grey |
Recommended for high pressure hydraulic service, steam and water. Abrasive against soft metal in dynamic applications under high pressure. |
-200
+260 |
0.08
|
10 |
05 |
PTFE/Carbon/
Graphite |
Black |
Similar to code 03 but increased wear resistance. Excellent in steam and water under severe conditions. Very good extrusion resistance at high temperature. Excellent material for back up rings. |
-250
+320 |
0.10 |
6 |
06 |
Premium PTFE |
Black |
Excellent material for extreme dynamic conditions. Combinations such as high temperature, pressure, speed and dry running. Excellent in water and water based solutions. Abrasive against soft metals. |
-250
+300 |
.09 |
1 |
07 |
PTFE/Bronze |
Brown |
Good abrasive resistance. Excellent in hydraulic applications. Not recommended for rotary applications. Good for high pressures. |
-150
+290 |
0.08 |
5
|
08 |
PTFE/Polyester |
Tan |
Special compound for high temperature applications. Recommended for low to medium speed applications running agains soft metals. |
-240
+340 |
0.13 |
3 |
09 |
Ekonol filled
PTFE |
Brown |
Special compound with superior head and wear resistance characteristics. Non abrasive. Recommended for low to high speed running against soft metals. Not good in water. |
-250
+340 |
0.15 |
3 |
10 |
UHMW-PE |
White |
Excellent wear material but limited heat and chemical resistance. Excellent for cryogenic temperatures. FDA approved. |
-250
+80 |
0.11 |
4 |
11 |
PTFE/Glass/
MOS2 |
Grey |
Similar to code 04 but softer for improved sealing at lower pressure. Can be abrasive running against soft metals |
-250
+300 |
0.09 |
1 |
12 |
PTFE/Graphite |
Black |
General purpose material with good heat and wear characteristics. Good in water, non lubricating fluids and compatible with all hydraulic fluids and most chemicals. |
-250
+300 |
0.09 |
5 |
13 |
PEEK |
Tan |
A high modulus material with excellent high temperature resistance. Excellent for back-up rings only. |
-70
+250 |
N/A |
N/A |
15 |
Filled PTFE |
White |
A food/drug compatible blend. Application tests should be carried out for prolonged use in water. FDA approved. |
-250
+300 |
0.11 |
5 |
17 |
15% Glass Filled PTFE |
White |
Typically used for backup rings. Abrasive in dynamic applications running against soft metals. |
-200
+270 |
0.10 |
3 |
21 |
Moly Filled PTFE |
Dark Grey |
Typically used in dynamic vacuum applications and in rotary duty in electronics industry. |
-200
+250 |
0.09 |
10 |
22 |
Modified PTFE |
white |
Excellent for static applications, particularly good in cryogenic duty using thin gases, FDA approved. |
-260
+230 |
0.09 |
150 |
23 |
Carbon/Peek Filled PTFE |
Dark Tan |
Useful high pressure/ high temperature material |
-120
+300 |
0.1 |
5 |
Ekonol is a registered trademark of Sohio Co.
Other materials available. Use will be determined by our technical department in consideration of specific application.
|
Spring Materials:
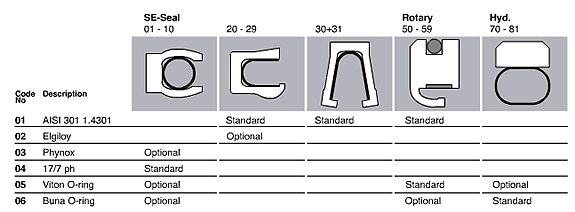
Standard Materials:
301/304 SS for cantilever spring energized seals
17-7 PH SS for helical spring energized seals
Specials Materials*:
316 SS, Elgiloy, Inconel, Phynox, Hastelloy
Specials Seal Energizers*:
Buna-N or Viton O-ring, "Angled Coil Spring", silicone encased springs, etc.
*please consult our technical sales group for availability
|